Mitsubishi Paper Mills, PM7 in Hachinohe mill, Japan

“A great reduction in production costs and increase in productivity”
Paper machine
- Grades: Base paper, fine paper, book paper, LWC paper
- Speed: 1,300m/min
- Production: 13,000 t/month
- Wire width: 5,800 mm
Challenges
After switching to a dual polymer retention system and ECF pulp, first pass retention decreased and the consumption of retention aids increased. This called for a new chemical mixing system to:
- reduce the consumption of retention aids
- improve the first pass retention
- prevent the collection of scale and dirt
- prevent sheet formation problems
Our solutions
- TrumpJet Flash Mixing stations for retention aid polymers (A-PAM and C-PAM).
- Moving A-PAM mixing location after the screen
Results
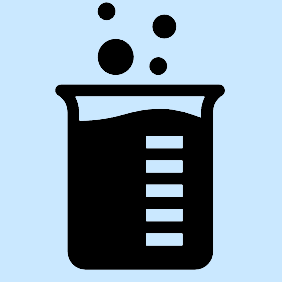
40% retention aid savings
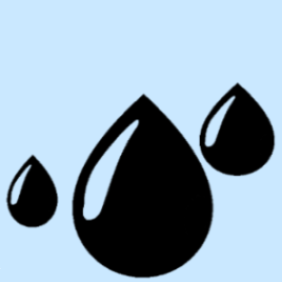
90 m3/day fresh water savings
(reduction of dilution water for A-PAM line)
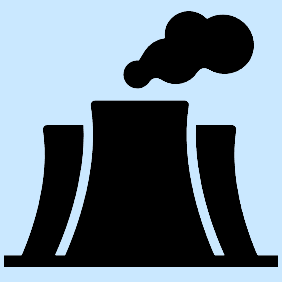
2,540 kWh/day energy savings
(to heat fresh water from 11.8°C to 37°C)
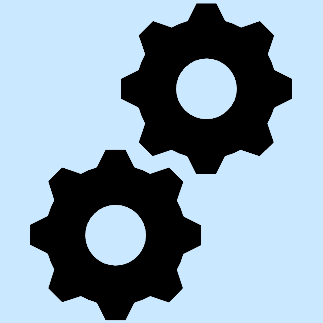
3.5% production increase
8% total first pass retention increase
12% ash first pass retention increase
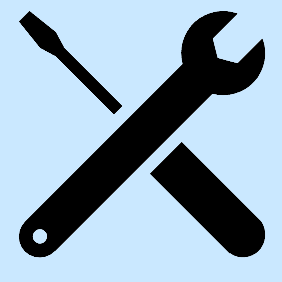
33% prolonged lifetime of felt and wire
33% extended shut down cycle
(30 days → 40 days )

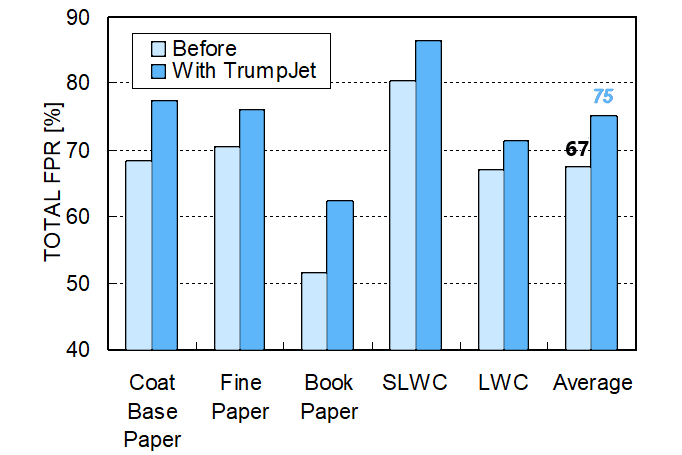
Conclusion
Due to success of the first TrumpJet® injection mixing installation and the potential to decrease chemical consumption even more, a decision was made for a “step two” of the project: injection mixing of C-PAM + AKD after the screen with TrumpJet Chord.
The great reduction in production cost and 3.5% increase in productivity lead to new repeat orders for the other lines.
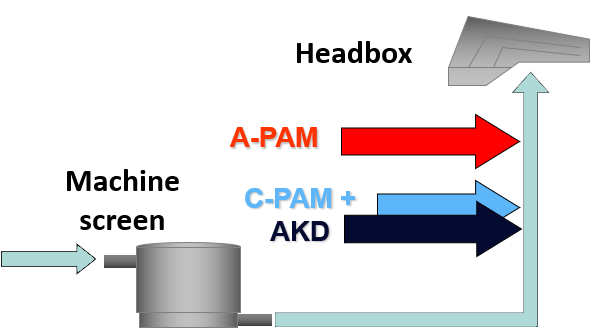
Considering chemical mixing optimization?
We can help you to lower production costs, improve machine runnability and product quality, while reducing the environmental impact of your production, and much more.