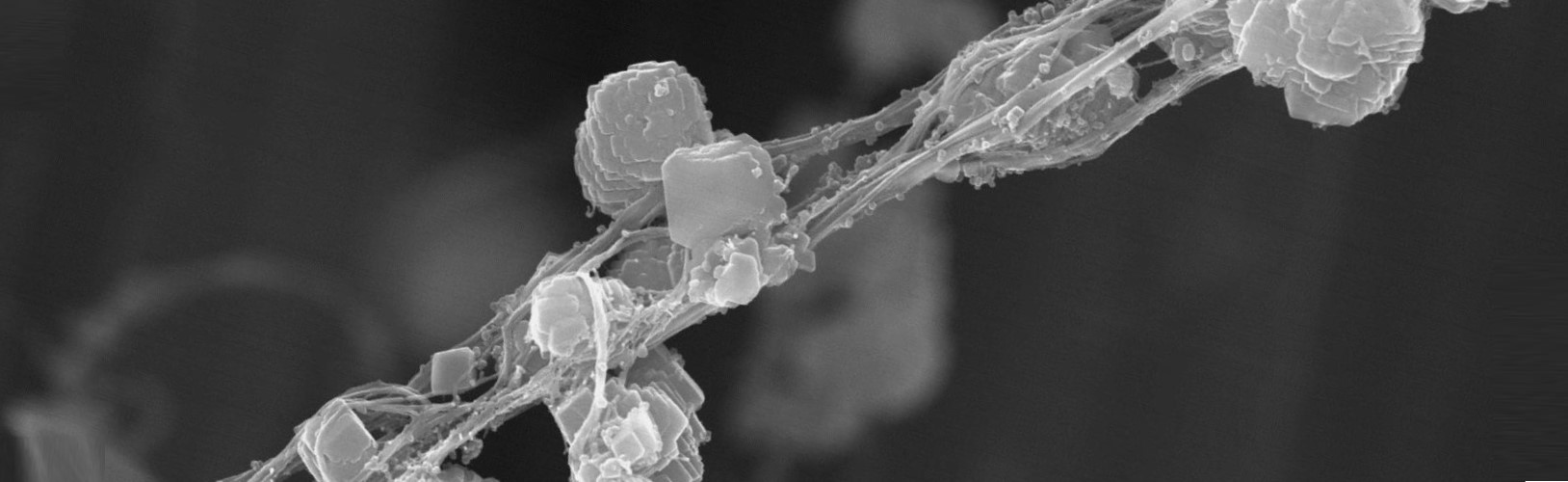
In-Line PCC™

High-quality PCC composite from an integrated process
In-Line PCC™ is a machine-integrated process that generates a new type of calcium carbonate filler-fiber composite – a novel raw material competitive in quality, price and technology. The process offers low operating costs, improved machine runnability, increased efficiency, high quality of the end product.
In-Line PCC™ benefits
Competitive advantages with minimal investments
- Attractive and price-competitive filler material
- Substantially lower investment and operative costs
- no need to invest in a separate PCC satellite production plant with long-term supplier contract
- Powerful fiber loading effect
- Very high retention of filler and fines
- Retention aid consumption reduces up to 80 %
- Less filler penetrates through wires resulting in less wear and longer lifetime of machine fabrics
- Excellent strength and optical characteristics of the sheet
- Cleaner paper machine approach flow system
- Significantly improved web formation
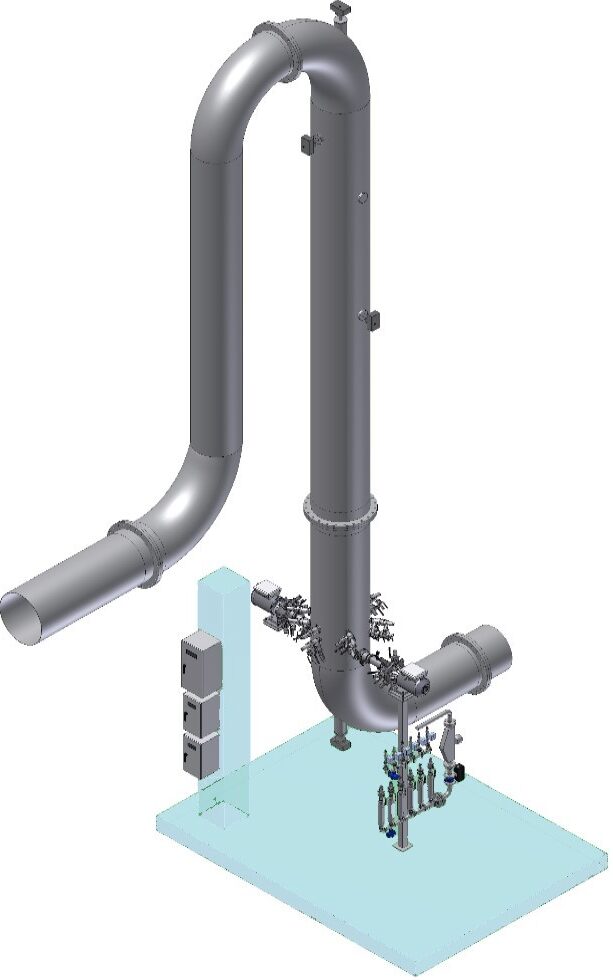
In-Line PCC™ process
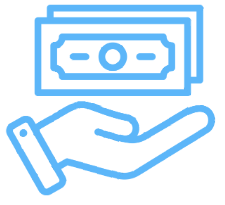
Low investment and operating costs
In-Line PCC technology is a simple and straightforward filler manufacturing process integrated directly into the paper machine short circulation. There is no need to invest in a separate PCC satellite production plant with long-term supplier contract. The production system can be easily operated by the mill personnel.
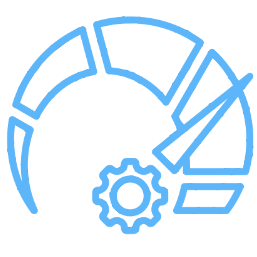
High speed, seamless integration
The In-Line PCC process is extremely fast and therefore it can be integrated directly to paper or board production line. The conventional calcium carbonate precipitation process might take hours, but the In-Line PCC Flash Mixing Reactor completes the precipitation reaction within less than one second.
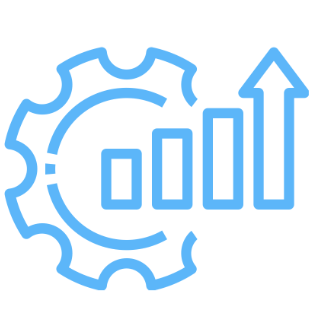
Clean process, excellent runnability
The In-Line PCC™ process binds and eliminates interfering colloidal substances, reducing the solids content and COD of white water. The cleaner PM approach flow system improves machine runnability and the efficiency of wet end additives. It also facilitates the operation of the mill wastewater plant and reduces the need for waste disposal.
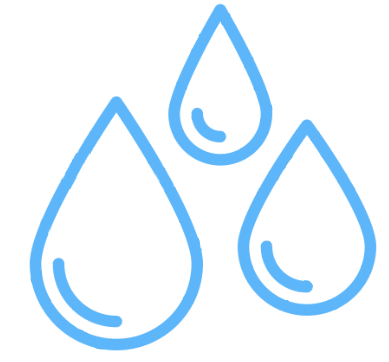
Fresh water savings
The lime slaking process can utilize mill filtrates such as clear filtrate. This cuts down the need of fresh water and closes the PM water circulation system at a much more efficient level. Thus, the fresh water consumption per paper ton is significantly reduced.
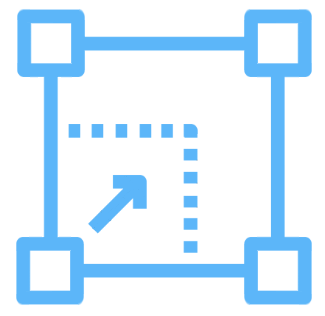
Adaptable to different capacities
The process fits easily both large and small production lines, adapting effortlessly to different capacities. This allows smaller paper and tissue lines as well as, for example, a white top board ply to exploit the benefits of the In-Line PCC filler.
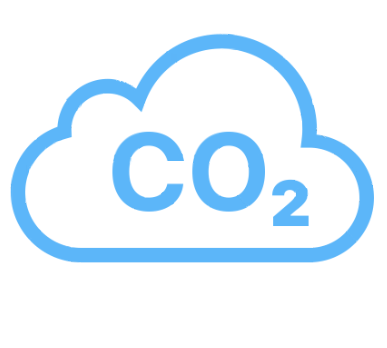
Possibility to use reclaimed CO2 emissions
The In-Line PCC concept exploits commercial liquid carbon dioxide, but it can also use carbon dioxide recovered from fumes of the boiler plant or lime kiln.
In-Line PCC™ material
- High-quality, price-competitive filler-fiber composite
- PCC crystals are firmly anchored to fibers and fibrils
- Average PCC crystal size is very small
- Uniform filler distribution in paper web
- High robustness of the composite structure
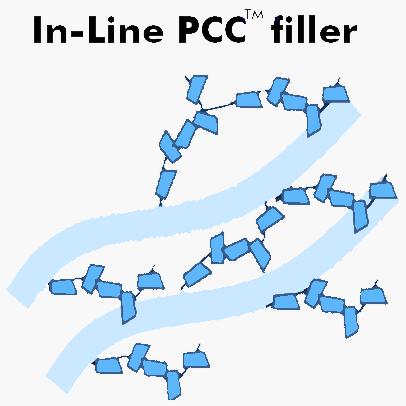
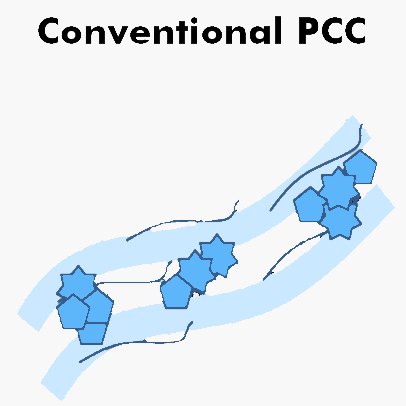
Excellent optical and strength properties
The uniform filler distribution in paper web and the small PCC crystal size enhance paper brightness, light scattering and opacity, improve formation, and lead to excellent strength properties of the paper web.
Opportunity to increase the filler content of paper
In-Line PCC provides an opportunity to increase the filler content in paper. The cost-saving potential especially in printing paper production is significant.
Facilitated dewatering and effective bulk control
The filler-fiber composite opens the structure of paper web and eases dewatering, which lowers production costs. The more open sheet structure allows to adjust and control bulk, especially for copy papers.
The products of Wetend Technologies Ltd. are protected with numerous international patents and patent applications.
Considering chemical mixing optimization?
We can help you to lower production costs, improve machine runnability and product quality, while reducing the environmental impact of your production, and much more.